Professional repair technicians are trained to work with generators, minimizing the risk of damage or injuries. They also have specialized tools and equipment that help them address issues quickly and effectively.
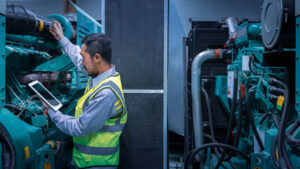
A poorly-functioning generator can cause costly repairs, so it’s important to schedule regular inspections and maintenance. This will prevent problems before they become costly, and can save you money on energy costs over time. Contact Generator Repair Houston for professional help.
If your generator is tripping its breakers or experiencing a drop in voltage, it could be due to damaged wiring. Over time, wires in a generator can become frayed or corroded and it’s important to check for any signs of damage on a regular basis. Keeping an eye out for any issues with your generator will help you repair or replace them before they lead to more serious problems.
Whether you are using a home standby generator or a portable generator, it is a good idea to inspect it regularly to prevent any problems that may arise. Some problems can be easily addressed by a home owner, and others require a professional to resolve. When a generator is not working properly, it’s crucial to quickly address the issue to avoid having to rely on expensive replacement services.
The generator consists of an engine that drives an alternator, which produces electrical power through electromagnetic induction. The engine can be powered by different fuel sources, such as gasoline, propane gas or diesel.
A generator can experience a wide range of problems, including starting issues, electrical glitches and battery or circuit breaker malfunctions. It’s also important to maintain the generator by inspecting fuel levels, spark plugs and air filters. A multimeter, screwdrivers and other tools are essential to repairing a generator, and you should have safety gear on hand to protect yourself from potential hazards.
Often, wires in a generator can become damaged by lightning strikes, or they may be subjected to excessive wear and tear over time. A common problem is a broken neutral wire in a three phase connection, which can be caused by lighting or by an imbalance between two phases and the neutral.
This type of problem can usually be repaired by applying heat-shrink tubing over the exposed section of the wire. The tubing will start to shrink almost immediately, and it’s a good idea to cut the tube twice as long as the damaged area to ensure that it will cover the entire end of the cable. This method works best with cables that have ends that are the same size as the cable itself, such as automotive wires or household appliances.
Fuel Failure
In many cases, a generator will simply run out of fuel. Fortunately, this can usually be fixed by filling the generator and testing it again. Alternatively, it may have a leak, which can be identified by inspecting the system for loose or broken connections and ensuring that flexible lines are in good condition. Fuel deterioration can also contribute to generator failures, so it is important to use fresh fuel and keep an eye on the fuel gauge.
Another common reason for generator failure is a lack of maintenance. A generator should be inspected and tested at least monthly, including exercising the transfer switch and running the generator for 30 minutes. This helps to detect and correct a wide variety of mechanical problems that can cause a generator to fail, such as a faulty recirculating breather or an oil leak.
Stator winding faults often occur due to the fact that the stator is exposed to high electro-dynamic stresses during operation. These faults can be caused by a wide range of factors, such as faulty or damaged connections between coils, current leakage faults from the coils to the core, and corrosion of the winding insulation. The best way to avoid these issues is to have the generator checked and serviced regularly, preferably by a trained technician.
Coolant leaks are another common problem in generators, which can result in overheating and damage to key engine components. Frequently inspecting hoses and belts, ensuring that they are tight and in good condition, and keeping an eye on the chemical balance of the coolant can prevent this problem from occurring.
Finally, problems with circuit breakers and fuses can lead to a generator’s failure to start. If these components are not working properly, the engine will not be able to engage its starter motor and rotate at high speeds, which is necessary for starting the generator. These problems can be caused by worn-out brushes, solenoid issues, or electrical system problems, among other things. Keeping the generator’s software up to date can also help prevent these types of failures, as older programs can have compatibility issues or bugs that may hinder the function of the generator.
Worn Belts
Think of EPDM belt wear the way you think of tire tread: Over time, it gradually loses its grip. This causes the belt to slip, which puts a strain on other components within the system and can cause them to fail. If you’re experiencing this problem, it is likely that you need a new generator belt.
Often, the first sign of a worn belt is a squeal. This is caused by the belt rubbing against a pulley that has become misaligned or is wearing out too quickly. This can also happen when a belt is tightened too tightly, which causes it to slip. Slipping belts not only affect the performance of the generator and water pump, but they also put extra stress on those components’ bearings, which can cause them to wear out prematurely.
A glazed appearance on the surface of the belt is another common sign that it’s time for a replacement. This usually occurs on the side of the belt that touches the accessories and support pulleys. This is most often caused by misalignment of the pulleys and tensioner, but can be the result of a loose cotter pin or other debris that has entered the engine bay.
Cracking is another common symptom of a worn belt. This is most frequently seen on the backside of the belt, which rubs against the pulleys and backside idlers. Cracking is often caused by excessive heat, although it can be the result of other factors like wrong belt cross-section, improper belt tension and misaligned pulleys.
You can check the condition of your belt by spinning each pulley and listening carefully. Make sure they spin freely and are quiet. You can also check the condition of the tensioner and any idler pulleys that don’t drive anything, such as power steering. They should not move in or out at all, and if they do, it’s a good idea to replace them. Lastly, take the belt off and look at the inside surface of the ribs. The ribs should not be cracked or worn away, and any rubbing can cause the belt to break.
Dirty Air Filter
If your generator’s air filter is dirty or clogged, it can restrict the flow of oxygen into the engine. This can lead to reduced performance and efficiency, as well as a shorter lifespan for the generator. Dirty or clogged filters can also affect the fuel-to-air ratio in the combustion chamber, which can cause your generator to surge and stall frequently.
To clean the air filter, turn off your generator and let it cool. Locate the air filter cover and remove it. Use compressed air or a soft-bristled brush to remove excess dirt and debris from the filter. You can also use a mild detergent with water to clean your air filter, but be sure to rinse it thoroughly to avoid any soap residue.
Another common problem that may prevent your generator from starting is a dirty spark plug. This can cause problems such as poor ignition, excessive fuel consumption, and black smoke. To fix this, remove the spark plug and look for sludge or dark carbon deposits that are preventing it from firing. If you find that the generator still doesn’t start, replace the spark plug.
Carburetors are delicate and complex components, and it’s not recommended that you try to clean them yourself unless you have experience working on engines. You can however, clean the carburetor’s float, needle valve, and venturi. For this, you will need a carburetor cleaner and some tools such as a screwdriver, wrench, and wire cutters. It’s also important to make sure that the generator is turned off and completely cooled before you start to work on it.
Regular cleaning and maintenance are vital for a long-lasting and effective generator. If you’re noticing signs that your generator isn’t performing at its best, be sure to check the owner’s manual and website for cleaning and maintenance recommendations.